CHAPTER 1: Vacuum: An Enabling Technology
1.3.4 Thin Film Deposition by Metal Evaporation
1.4 Benefits of Creating a “Vacuum”
1.6 Sources for Information on Vacuum Technology
Chapter 1 introduces the concept of vacuum and why it is important to be able to create a vacuum condition in a controlled space. After you read this chapter, you will be able to:
- Identify a variety of everyday items that are manufactured using vacuum technology.
- Define the meaning of the word “vacuum” as it will be used in this text.
- Describe some common processes enabled using vacuum technology.
- Explain reasons why a vacuum condition is beneficial in manufacturing and research processes.
- Describe different ways to create a vacuum condition.
- Identify other resources that provide information on vacuum technology.
A Brief Vignette
The impact of vacuum technology on today’s world is extensive. But like the air that surrounds us, the use of vacuum technology is mostly invisible to us, so we don’t necessarily appreciate that it exists despite how much it influences our everyday lives.
You look out the window and it’s raining outside. You’ve been studying awhile on the computer and are ready for a break. You turn on the lights in the kitchen, pour a glass of water from the faucet and open a bag of pre-popped popcorn. You decide to watch a show on television this evening. You use the remote control to turn on the TV. As you scan through the viewing options, you see an advertisement for a pair of sunglasses you want to buy. Out of the corner of your eye, you notice that one of the framed pictures hanging on the wall next to the TV is crooked. Your hand moves to straighten the picture, but you brush across a spider web. Ugh! Need a vacuum cleaner to get rid of that! Then your cell phone goes off. Well, so much for your TV time!
For many of the products mentioned in our vignette, vacuum technology played an important, if not critical role, in its manufacture. In the case of the window, faucet, bag, sunglasses, and framed pictures, it is one or more thin material coatings on the surface which enhance the function of each product. In the case of the computer, television, remote control, and cell phone, vacuum plays a critical role in the manufacture of the integrated circuits that determine their function. And, the kitchen lights, if incandescent or fluorescent, would not work if the air inside the bulb were not removed. Without vacuum, none of these products would exist in their present form.
1.1 Introduction
Vacuum technology is an “enabling technology” that makes it possible to achieve other goals. This concept was expressed by Lars Montelius, President of the International Union for Vacuum Science, Technique, and Applications (IUVSTA) when he shared his view on the creative nature of vacuum science and how vacuum has enabled innovations that help to build a more sustainable society. Here is a quote from an article in the publication 2018 Physics World Focus on Instruments and Vacuum:
“Vacuum systems are used in all kinds of equipment, and not only in the sciences. There is a long history of using vacuum for industrial machines and processes. Within the sciences, vacuum is important if you want to understand materials at a very small scale, because to do that you need very clean and stable conditions. In industry, one of the major applications is in industrial machines. For instance, vacuum is used to lift, position, and move objects. Simply speaking, without vacuum many industries would not exist. An example is the semiconductor industry. Once upon a time, the electronics industry ran on vacuum tubes: vacuum was an essential requirement for switching electrical currents. Although these switches have been replaced by solid-state electronics, manufacturing the electronics and circuits still requires vacuum conditions. I think vacuum is one of the most important elements of modern society, but it’s a paradox because vacuum itself is maybe not so important – it’s what you do with it that’s important. Vacuum is an enabler.” (1)
1.2 What is “Vacuum”?
You probably have a notion of the meaning of the term “vacuum.” As a noun, it can refer to a “vacuum cleaner” or some other contraption that picks up objects. In another sense, one might say that when someone leaves a group, their departure creates a “vacuum” in the group. So, with multiple definitions, and uses, for the term, it makes sense for us to define how we intend to use it in our discussions ahead.
In the ideal sense, a vacuum is a space that contains absolutely nothing, a space totally devoid of matter. However, in actual practice, such a perfect vacuum does not exist, even for the best vacuum systems. Under the best of vacuum conditions, a chamber still contains hundreds of thousands of gas molecules per cubic centimeter. A variety of useful processes are accomplished under very different levels of vacuum. So, in this sense, a vacuum is created when gas molecules are removed so that the density of gas molecules in an enclosed space is less than the density of molecules in the surrounding environment.
The definition of vacuum for the purposes of this text is a space partially emptied (to the degree necessary to support a process) by artificial means (using a vacuum pump). This results in a volume containing far fewer gas molecules than the same volume in the surrounding atmosphere, that is, a degree of rarefaction below atmospheric pressure. If the surrounding atmosphere is at normal atmospheric pressure, then a vacuum exists if the density of the gas molecules in the chamber is less than the density of gas molecules outside the chamber in the ambient atmosphere.
1.3 Vacuum as an “Enabler”
In this section, we will examine examples of how vacuum “enables” various processes that benefit our lives today. We will examine how vacuum is used in food preservation, in thermal insulation, in surface coating materials, and in manufacturing processes used to manufacture integrated circuits.
1.3.1 Food Preservation
There are three things that cause food to deteriorate: heat, water, and oxygen. Vacuum sealing, freeze-drying and proper packaging overcome all three of those factors to allow long term food storage, up to 15 to 25 years in some cases. Furthermore, freeze-drying food causes little damage to the nutritional value of the food being preserved compared to other methods that use higher process temperatures, like canning and dehydration.
Vacuum sealing removes air from the package containing the food prior to sealing. The intent of vacuum sealing is to remove oxygen from the package to extend the shelf life of foods, thereby limiting the growth of aerobic bacteria or fungi. Vacuum sealing can also reduce “freezer burn” which occurs when the surface of the food dehydrates while it is frozen leading to a dried, leathery appearance and a change in flavor and texture. Figure 1.1 shows a vacuum sealer that can be used at home.
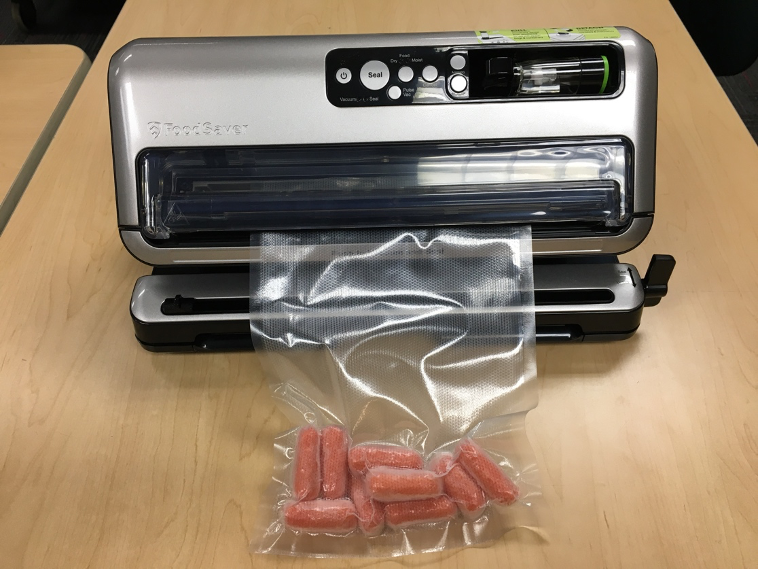
One example of a freeze-dried food item is astronaut ice cream, a slab of ready-to-eat dehydrated ice cream like the one shown in Figure 1.2. Unlike regular ice cream, astronaut ice cream can be kept at room temperature without melting. It was first developed by Whirlpool Corporation under contract to NASA for the Apollo mission, but it was never actually used on any Apollo missions. Other freeze-dried foods were developed to reduce the weight of food by removing its water and oxygen content. Lighter-weight foods packaged for a longer shelf life could be sent on long-duration spaceflights.
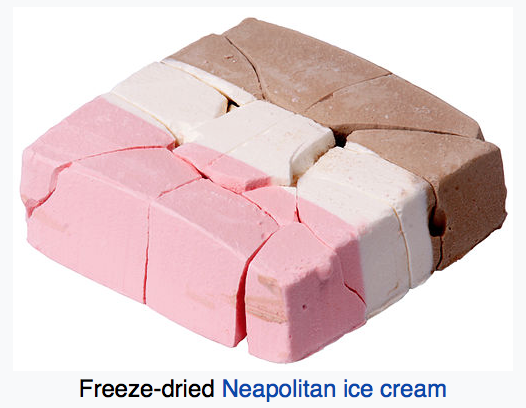
Freeze-drying, also known as lyophilization, is a dehydration process that removes water from a frozen food. To make astronaut ice cream, the ice cream is placed in a vacuum chamber and frozen until the water crystallizes. Air is then evacuated from the chamber to create a partial vacuum. The crystallized water then begins to sublimate, that is, change from a solid to gas. Heat can be applied to speed up the sublimation process. And finally, a freezing coil captures the vaporized water. This process continues for hours and eventually results in a freeze-dried slice of ice cream.
1.3.2 Thermal Insulation
Vacuum enables “thermal insulation”. Thermal insulation retards, or slows down the flow of thermal energy. Consider a simple vacuum flask. You might commonly refer to it as a “thermos bottle.” It can be used to keep cold drinks cold, and warm drinks warm. Thermos bottles come in a variety of designs, but each design’s construction is essentially the same. As shown in Figure 1.3, a thermos bottle is basically two chambers, historically glass, but now typically metal, one inside the other with a partial vacuum between the two chambers.
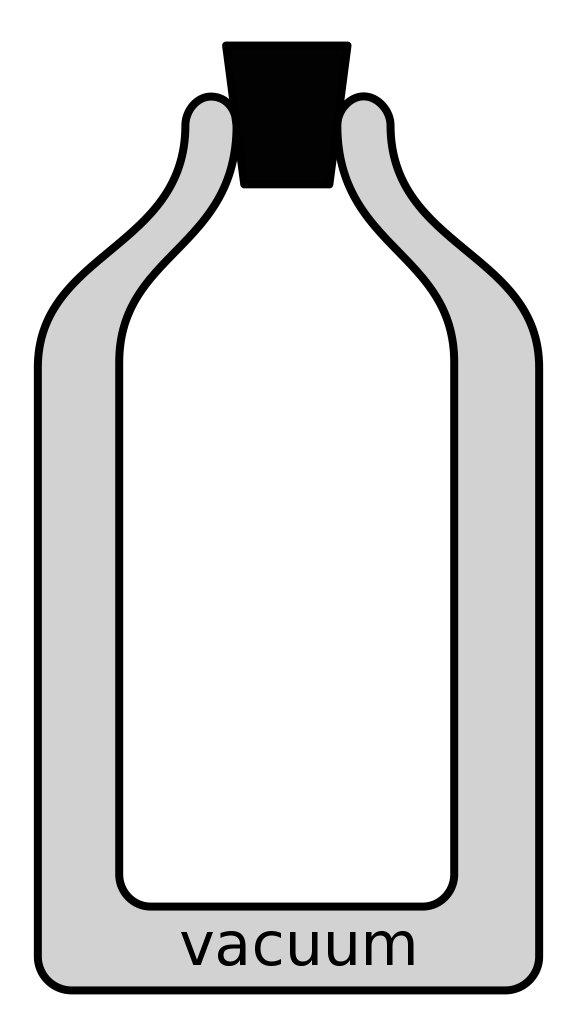
What happens when the contents of the flask are surrounded by air at atmospheric pressure? The contents within the flask might be cold with warm or hot air outside the flask, or the opposite, hot inside and cooler or very cold air on the outside. In either case, a temperature difference exists between the surrounding air and the contents of the vacuum flask. Heat transfer occurs when molecules collide with each other and transfer energy. Heat flows from the warmer region to the colder region. A space in which more molecules are present supports a higher rate of heat transfer than the same space with fewer molecules. Different gas molecules have different energies, so the type of gas molecules present in the space also affects the rate of heat transfer.
How does a vacuum condition impede heat transfer? Suppose we have filled the thermos bottle with a cold liquid. Between the inner and outer surfaces, most of the air is removed to create a vacuum. If we remove enough of the air molecules, the air molecules will be able to travel between the inner and outer surfaces without colliding with another air molecule. So, an air molecule hits the warmer outer surface and picks up some energy. After rebounding off the outer surface, the air molecule then travels toward the inner surface where another collision results in a transfer of energy from the air molecule to the inner surface, providing energy to warm the cold liquid. The goal is to minimize the number of gas molecules transferring heat energy from the outer surface to the inner surface. The fewer the air molecules in the vacuum space, the slower the heat transfer to our cold liquid, and the longer our cold liquid will remain cold.
1.3.3 Vacuum Gripping
Vacuum gripping is useful in lifting, moving, or holding objects in place. Consider a simple suction cup. Air is removed by pressing a flexible membrane against a surface. Then the membrane is pulled away from the surface, expanding the volume that is captured underneath the membrane. The pressure in the volume between the flexible membrane and the surface is lower than the pressure exerted on the opposite side of the surface keeping the membrane in place.
For example, the cell phone holder pictured in Figure 1.4 uses a suction cup at its base to adhere to a smooth surface. The cell phone holder consists of a flexible base with a moveable diaphragm, a lever attached to the diaphragm, a ball joint to allow positioning of the holder, and the cell phone holder. When the cell phone holder is placed on a non-porous surface and the lever is moved down, it mechanically pulles the diaphragm away from the surface creating a vacuum by expanding the space with trapped air molecules. The atmospheric pressure of 14.7 psi now provides the holding force for the cell phone holder. To release the holder, the lever is moved up, or away from the base of the holder, and the space created by the deformed diaphragm shrinks so that the holder can be moved, or re-positioned.
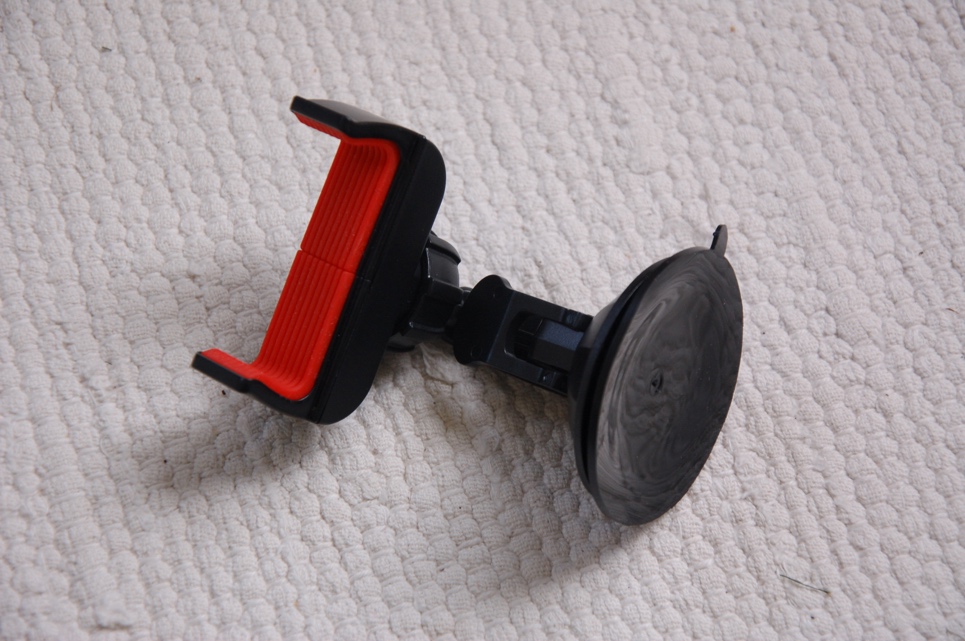
Glass handles operate in a manner similar to the cell phone holder. They allow a person to hang onto a large sheet of glass, for example, a large storm window. The glass handle is positioned on the pane of glass and a lever lifts the diaphragm creating a void next to the glass. Again, atmospheric pressure applies pressure to the glass handle, keeping it securely attached to the glass. Figure 1.5 shows a glass handle with the diaphragm base.
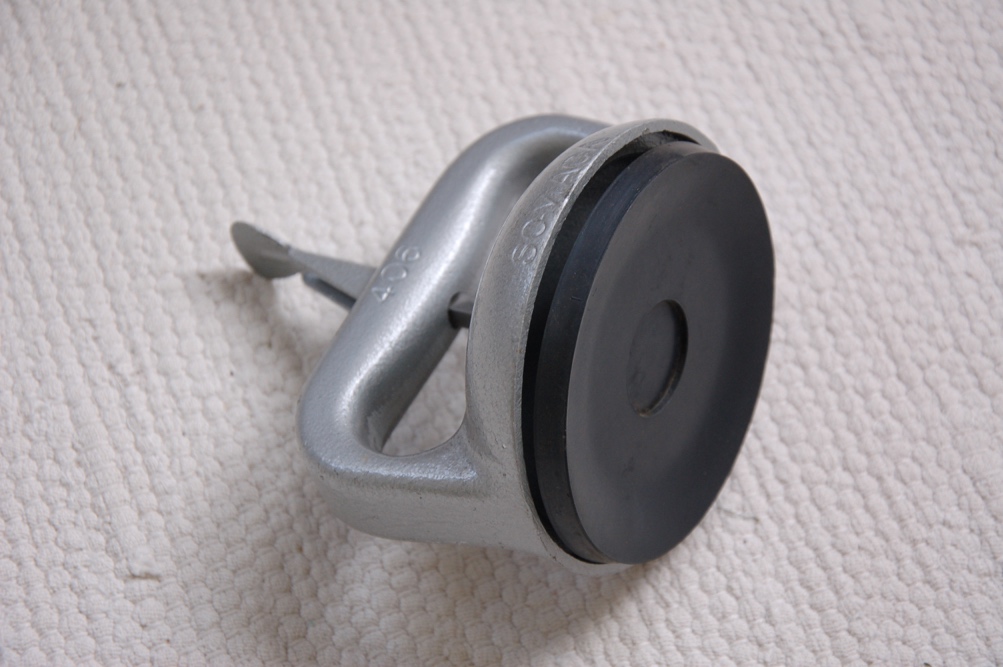
A vacuum chuck is another example of vacuum gripping and is primarily used on non-ferrous materials, for example, glass, plastic, copper, aluminum, and even wood. In a vacuum chuck, air is pumped from a cavity behind the workpiece and again atmospheric pressure provides the holding force. In Figure 1.6, vacuum chucks are placed under a wooden workpiece and the vacuum holds the workpiece while it is milled. Vacuum clamping is a technique to prevent marring or damage to a workpiece that might occur if it was otherwise mechanically clamped in place. Vacuum gripping can also allow greater access to the work piece being machined.
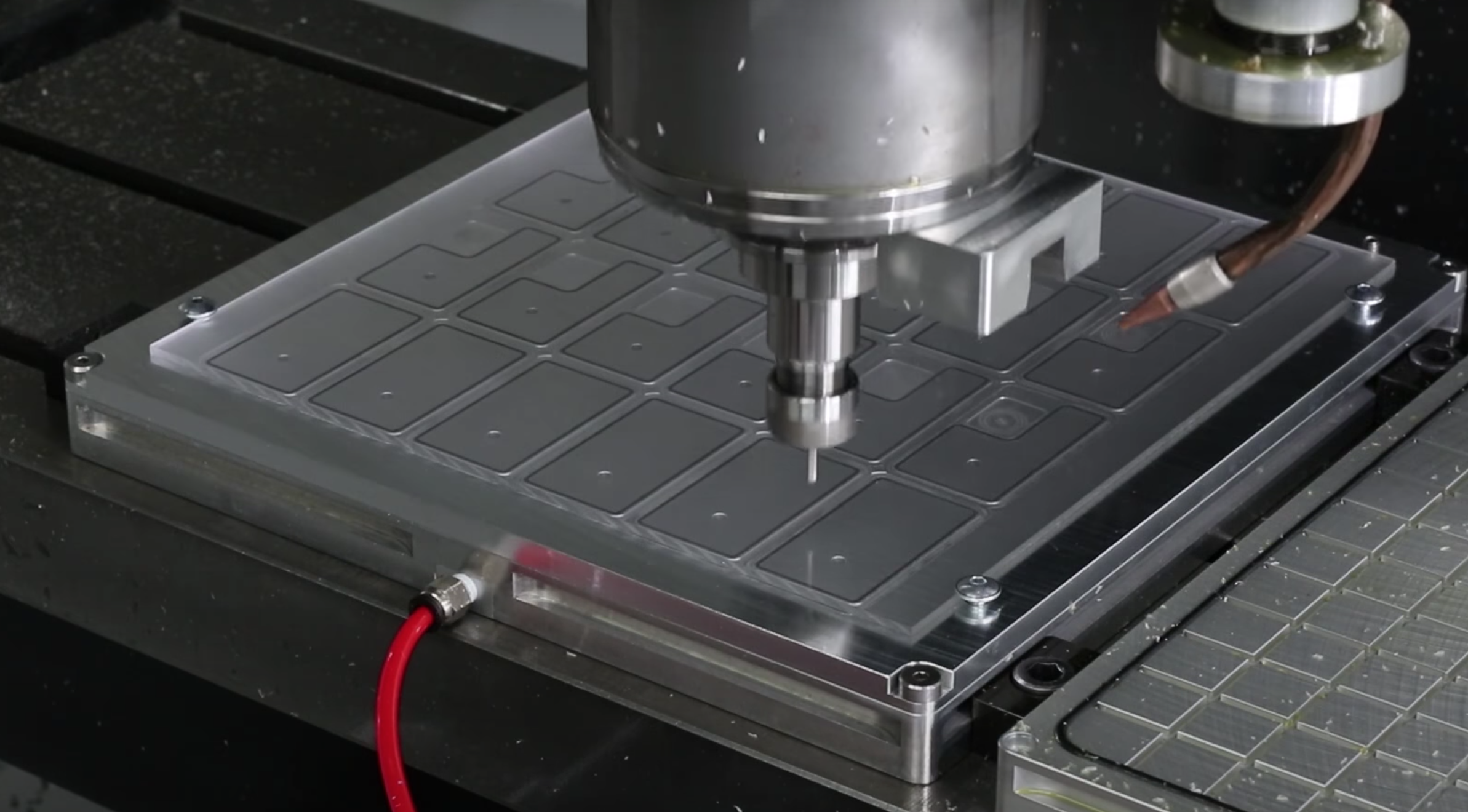
1.3.4 Thin Film Deposition by Metal Evaporation
Vacuum systems are used to establish conditions necessary to carry out manufacturing processes. Consider metal evaporation. In this manufacturing process, the goal is to coat a surface with a thin metal layer. In semiconductor manufacturing this metal layer can be patterned to form the interconnects between various points on a silicon wafer.
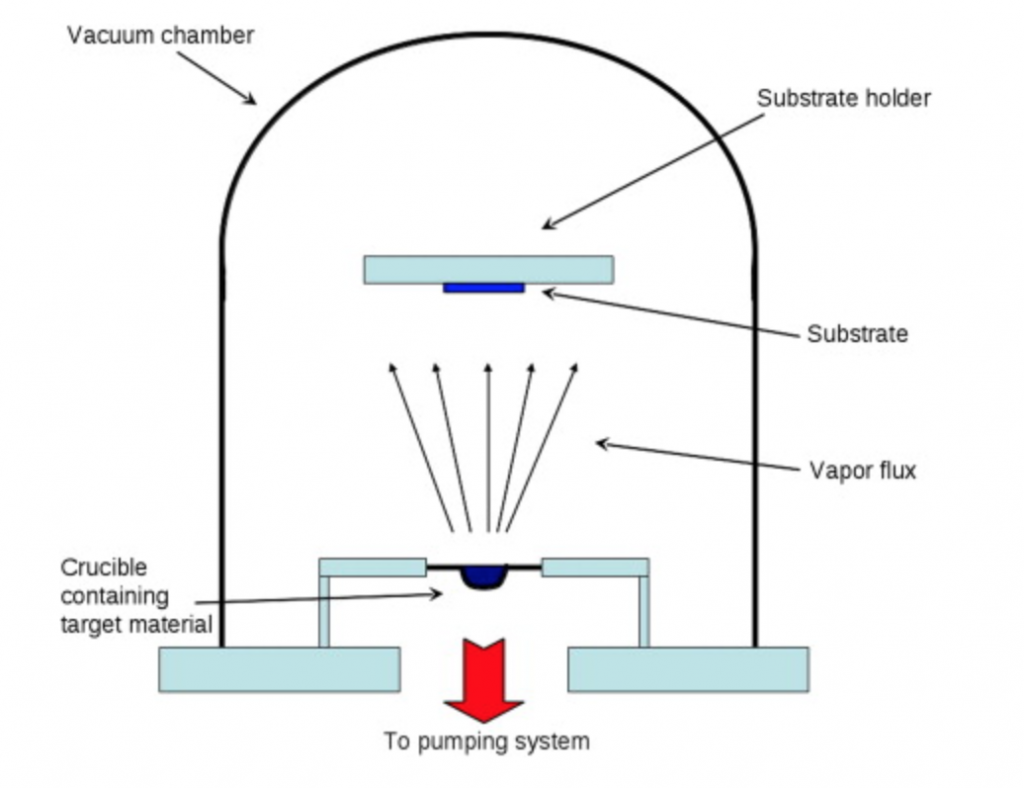
Public domain, generated by CNEU staff for free use.
The basic evaporation process involves two steps: (1) in a crucible, a hot metal source evaporates creating a vapor of metal atoms and (2) the metal atoms travel to the substrate and condense on the substrate’s surface. However, before this two-step process is performed, the chamber is put under vacuum. A vacuum condition ensures that metal atoms, once vaporized can travel to the substrate without being impeded by other gaseous atoms or molecules, or colliding with foreign particles that may react with them. When evaporation is performed in a poor vacuum, or close to atmospheric pressure, the resulting layer of metal is generally non-uniform both in thickness of the deposition and quality of the material deposited. Figure 1.7 shows a typical diagram of metal evaporator used for such processes.
One advantage of metal evaporation is that multiple substrates can be processed at the same time, but it does pose a challenge. Because the metal vapor originates at a point source, the evaporated metal atoms attack the substrate surface from a single direction. Protruding features can block the metal atoms and “shadowing” can occur. To limit this problem, a different thin film deposition process called “sputtering” can be used.
1.3.5 Other Examples
The examples of vacuum as an “enabler” described in Section 1.3.1 through 1.3.4 are just a few of the many processes where vacuum is used. Table 1.1 lists other processes carried out in each of three pressure regimes. This is by no means an exhaustive list, but it does give you a view of the breadth of applications where vacuum is used.
Table 1.1. Processes that use vacuum.
Rough Vacuum |
High Vacuum |
Ultrahigh Vacuum |
---|---|---|
Food Processing/Packaging |
Heat Treating |
Materials Research |
Freeze Drying |
Vapor Deposition |
Metallurgy |
Gas Lasers and Neon Signs |
Ion Implantation |
Surface Analysis |
Sputtering |
Surface Coating |
Molecular Beam Epitaxy |
Distillation |
Thermal Insulation |
Physics Research |
Electric Conduction |
Chemistry Research |
Space Research |
In many applications that require pressures in the high vacuum and ultrahigh vacuum pressure regimes, specialized tools and instruments are needed. For example, in the semiconductor industry, complex manufacturing tools are needed for chemical vapor deposition and ion implantation. These tools are composed of multiple subsystems, one of which is the vacuum subsystem. In other applications, specialized tools such as electron microscopes utilize vacuum to establish the operating environment in which measurements can be made. Vacuum technology and the application of vacuum is so pervasive in our world today that without vacuum technology, we would not have many of the products we use on a daily basis.
1.4 Benefits of Creating a “Vacuum”
We have described the types of applications enabled by vacuum technology such as food preservation, freeze-drying, thermal insulation and metal evaporation. Now, let’s examine why one would want to create a vacuum in a semiconductor manufacturing process, for example, chemical vapor deposition, sputtering, or ion implantation.
Removing gas molecules from an enclosure or process chamber achieves several objectives. First, it results in a cleaner process environment by removing potential contaminants. Contaminants can be particles as well as unwanted gases that, if allowed to remain in the chamber, can participate in the chemical reactions taking place in the chamber and ultimately, produce unwanted by-products. For example, if two gases are to react in a process chamber to deposit a coating on a silicon wafer, you don’t want the oxygen and nitrogen present in air to combine with the reactant gases. Therefore, before introducing the reactant gases into the process chamber, the air in the chamber is first removed from the chamber to reduce the amount of oxygen and nitrogen molecules present. After the desired chemical reaction has taken place, the unused reactant gases must be pumped out of the chamber before the chamber pressure can be brought back to atmospheric pressure and the wafer removed.
Second, creating a vacuum in a process chamber increases the mean free path (λ) of the gas molecules. The mean free path of a gas molecule is the average distance the gas molecule will travel before colliding with another gas molecule. As the chamber pressure is reduced, fewer gas molecules occupy the volume. When the number of gas molecules in the space is reduced, the molecules remaining in the space collide with each other less frequently as shown in Figure 1.8. This is important in manufacturing processes such as sputtering, evaporation, and ion implantation. In these examples, a high molecular density of gas molecules would impede particles from reaching the substrate, for example, a wafer.
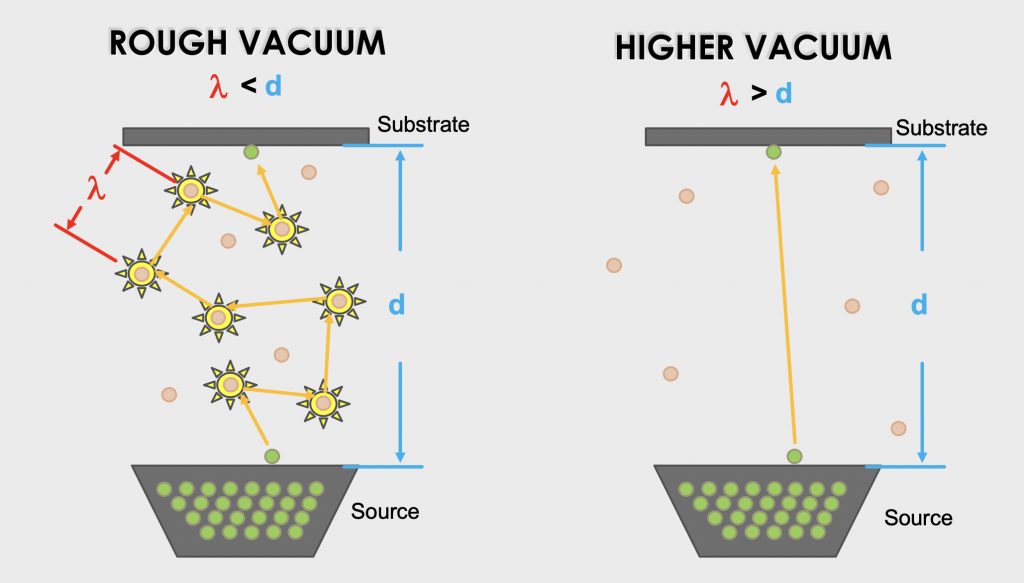
Third, creating a vacuum in a process chamber is a way of controlling the number of collisions of molecules against a surface, for example, a wafer. This is important when sputtering metal layers or in controlling the rate of film growth in chemical vapor deposition.
Fourth, creating a vacuum lowers the molecular density. Consider the case of the ordinary incandescent light bulb. If the inside of the light bulb were not first evacuated to remove air, any oxygen molecules left in the bulb when the filament is heated would react with the metal and the metal filament would burn up.
Fifth, creating a vacuum can result in a force that is useful in many manufacturing processes. For example, a force can be created to secure a wafer to a vacuum wand when the wafer has to be moved from one place to another, or to a chuck so that the wafer cannot move during a manufacturing process.
Sixth, creating a vacuum reduces the rate of heat flow. A reduction in pressure decreases the molecular density and hence, a reduction in the number of molecule-to-molecule and molecule-to-surface collisions. Fewer collisions result in less heat transfer.
Seventh, creating a vacuum can increase vaporization. Vaporization occurs when liquid molecules leave a surface and do not return. It works like this: if the chamber containing a liquid is evacuated, fewer molecules will be above the liquid surface. Thus, a molecule that evaporates from the surface of the liquid is less likely to collide with another gas molecule because there are fewer molecules in the space adjacent to the liquid surface. With fewer molecules present for collisions, vaporizing molecules travel enough distance from the liquid surface so that they cannot readily return to the liquid surface.
Finally, creating a vacuum can protect materials from reacting with air. To accomplish this, the chamber is first evacuated and then backfilled with an inert gas in order to remove as many reactive gas molecules as the process dictates.
Table 1.2. Benefits of a vacuum.
Benefits of a Vacuum |
---|
Produces a cleaner process environment |
Increases mean free path |
Controls the number of surface collisions |
Lowers molecular density |
Creates a force |
Reduces heat flow |
Increases vaporization |
Protects materials |
1.5 How to Create a “Vacuum”
In our discussion in this chapter describing how vacuum is an enabling technology, we have described several ways to create a vacuum. The simplest way to create a vacuum is to mechanically increase the volume of the enclosed space. The cell phone holder and glass handles are examples. Deforming a flexible diaphragm and pulling it away from a non-porous surface creates a space underneath the diaphragm with a gas density much lower than the atmospheric conditions above the diagram. However, for this to work, the seal at the edge of the diaphragm must be airtight.
Another way to create a vacuum is to lower the temperature of the gas in the enclosed volume. As the temperature is lowered, the gas molecules travel slower. When they hit the walls of the enclosed space, the force they exert will be smaller and there will be less pressure inside the closed space.
Now consider this, if the temperature is low enough and the gas molecules are able to freeze, that is, the molecules change directly from the gas state to a solid state, there will be fewer gas molecules in the gaseous state and they will be traveling slower, hence reducing the pressure. Consider a freezer in your home. Have you ever noticed that when you try to open the freezer door immediately after closing it, it often takes a little more force to open the door? This occurs because room air enters the freezer while the door is open. When you close the door, the room air is cooled by the cooling coils in the freezer and some of the water vapor may adsorb on the coils. This effectively reduces the pressure inside the freezer and the atmospheric pressure condition external to the freezer door, which remains constant, tends to hold the freezer door closed.
Another method to create a vacuum without lowering the temperature is accomplished by reacting the gas molecules with a chemically-reactive material to create a solid material. For example, within a closed chamber, the oxygen gas molecules in air will react with titanium to form titanium oxide, a solid compound that sticks to the chamber walls. By permanently removing oxygen from the gaseous state, the pressure level within the chamber is lowered to create a vacuum.
A more common and more efficient way of creating a vacuum is to displace, and remove, gas molecules from the chamber. There are many ways to accomplish this result using a variety of pumps of different sizes and designs. If the chamber pressure is near atmospheric pressure, mechanical pumps like rotary vane pumps, diaphragm pumps, and scroll pumps are used. As the gas density is reduced, these mechanical pumps become less effective in removing air from the chamber. To further reduce the chamber pressure, turbomolecular pumps, cryo pumps, and sublimation pumps are used. We will describe some of these pumps in more detail as we study various vacuum pressure regimes.
1.6 Sources for Information on Vacuum Technology
The material presented in these chapters is not intended to be an exhaustive treatment of vacuum and vacuum systems. Instead, it is intended to provide a fundamental understanding of vacuum systems for technicians and others who will be working with vacuum systems on a regular basis. Nevertheless, there will be times when you will want to research topics in vacuum technology in more depth.
1.6.1 Professional Societies
There are two major professional societies in the United States that focus on vacuum technology and its applications. They are the AVS and the Society of Vacuum Coaters (SVC).
AVS (formerly known as the American Vacuum Society): From the avs.org website,
As an interdisciplinary, professional society, AVS supports networking among academic, industrial, government, and consulting professionals involved in a variety of disciplines – chemistry, physics, biology, mathematics, all engineering disciplines, business, sales, etc. through common interests related to the basic science, technology development, and commercialization of materials, interfacing and processing area.
Founded in 1953, AVS is organized into technical divisions and technical groups that encompass a range of established as well as emerging science and technology areas. There are also regional chapters, international chapters and affiliates, and student chapters that promote communication and networking for professionals and students within a geographical region. AVS is comprised of approximately 4,500 members worldwide.
Society of Vacuum Coaters (SVC): From the svc.org website:
SVC is a non-profit, international, professional organization primarily devoted to coating and surface finishing using vacuum processes. Our organization consists of industry, academia and members from national research laboratories. Our industry membership includes coating companies, materials suppliers, process designers, equipment manufacturers. Our industry applies coatings and treatments to a wide variety of consumer and industrial products in all business sectors.
As with most professional societies, both AVS and SVC provide resources on their website that can be accessed for free.
1.6.2 Publications
Vacuum Technology & Coating is a readable monthly magazine on vacuum instrumentation, plasma processing, and thin film deposition. Each month, the magazine has feature articles on “Vacuum Technology,” “Photonics and Microelectronics,” “Thin Films and Materials,” “Nanotechnology,” and “Biotechnology.” Website: www.vtcmag.com
1.6.3 Vacuum Equipment Manufacturers
There are a number of companies that make and sell vacuum components, instrumentation, and related products. These companies include Pfeiffer Vacuum, Leybold Vacuum, MKS, Inc., Edwards Vacuum, Agilent, and Kurt J. Lesker Company. There is a wealth of information on vacuum on these websites. Here is a list of their websites:
- Pfeiffer Vacuum: Pfeiffer-vacuum.com
- Leybold Vacuum: leybold.com
- MKS: mksinst.com
- Edwards Vacuum: edwardsvacuum.com
- Agilent: agilent.com
- Kurt J. Lesker Company: lesker.com
1.7 Looking Ahead
Our study of vacuum systems will begin with a review of the behavior of gases. You may have studied gas laws in another class, for example, chemistry, so the material in Chapter 2 may be familiar. For a more in-depth treatment, a general chemistry text would be a good reference on this topic.
Chapter 3 will introduce vacuum systems and the components used to construct them. The presentation by design will be general. Chapters 4 and 5 will then provide a more detailed discussion of vacuum systems used in the rough vacuum regime and then the high vacuum regime. The discussion will follow a specific pattern and answer the following questions:
-
- What is the “gas load”? What gases must be pumped out of the chamber?
- How will the gas be removed from the chamber? What type of pump will best serve the need?
- How will the chamber pressure be measured? What type(s) of pressure gauges will be needed?
- How should the system be constructed? What types of fittings, valves, and other vacuum components will be needed?
- Are there other types of measurement and diagnostic equipment that will be needed, for example, residual gas analyzers and leak detectors?
Chapter 6 will describe an instrument called the residual gas analyzer. Unlike pressure gauges that require you to know what gas that is being pumped, the residual gas analyzer measures the partial pressure of each gas being pumped.
Chapter 7 will describe vacuum leak detectors. Unfortunately, leaks do occur, and leak detectors are used to find leaks in a vacuum system. In the case of vacuum systems, we will be looking at the ways that unwanted gas gets into the vacuum system.
Chapter 8 will provide a brief introduction to gas delivery and pressure control. The mass flow controller will be described along with several pressure control strategies.
Finally, Chapter 9 will conclude our discussion of vacuum systems with an overview of the safety issues related to vacuum systems.
Summary
Vacuum technology is an “enabling” technology making possible a wide range of manufacturing applications. Examples are food preservation, thermal insulation, vacuum gripping, metal evaporation and other semiconductor manufacturing processes. A vacuum environment is beneficial, and in many cases necessary, to produce certain products. Using vacuum allows us to control contamination, aid in material deposition processes, reduce heat flow, produce large forces, increase vaporization, and protect materials from reactions with air. There are several viable ways to create vacuum by using mechanical, chemical and thermal processes. These processes and corresponding technological solutions will be discussed in the following chapters.
References
Danielson, Phil. “Why Create a Vacuum?”. Vacuum & Thinfilm, July 1999, pp. 18-23.
Montelis, Lars. Vacuum the Enabling Technology, 12 Aug. 2018: http://www.physicsworld.com.
Quirk, Michael, and Julian Serda. Semiconductor Manufacturing Technology. Prentice-Hall, Upper Saddle River, NJ, 2001.
Tompkins, Harland G. The Fundamentals of Vacuum Technology. 3rd ed. AVS Monograph Press, New York, NY, 1997.
Questions and Problems
- How do you define vacuum? Draw an image that illustrates vacuum.
- Explain how a vacuum condition enables the food canning process. How do you recognize the can is sealed? How is the presence of a vacuum condition confirmed?
- Many food products are vacuum sealed. Provide two or more reasons or advantages for vacuum sealing food products.
- What’s another product where a vacuum condition usefully serves to slow heat transfer? Explain in general terms how slowing the rate of heat transfer benefits the product.
- Consider a pot of boiling water on a stove top. You pass a plate above the rising steam. Describe what happens and why.
- Pick one of the “Other Examples of Vacuum Processes” listed in 1.3.5. Explain the process in general terms. Roughly, what is the amount of pressure required for that process?
- Go to the latest edition of vtcmag.com. Identify a new product enabled by vacuum.
- Go to the website of one of the vacuum manufacturers listed. Identify some of the vacuum related products they sell.
- The following individuals are recognized to have made significant contributions to the development of vacuum science and vacuum technology. Use online resources to describe their work related to vacuum science/technology:
- Torricelli, Evangelista
- Pascal, Blaise
- Boyle, Robert
- Von Guerike, Otto
- Amontons, Guillaume
- Gay-Lussac, Joseph Louis
- Charles, Jacques
- Dalton, John
- Clausius, Rudolf
- Maxwell, James Clerk
- Boltzmann, Ludwig
- Sprengel, Hermann
- McLeod, Herbert
- Swan, Joseph
- Edison, Thomas
- Pirani, Marcello
- Gaede, Wolfgang
This work is supported by the National Science Foundation under grant number 2000454. Any opinions, findings, and conclusions or recommendations expressed in this e-book are those of the authors and do not necessarily reflect the views of the National Science Foundation.
Media Attributions
- Figure 1.1 © Nancy Louwagie is licensed under a CC BY-NC-SA (Attribution NonCommercial ShareAlike) license
- Figure 1.2 © Evan-Amos is licensed under a Public Domain license
- Figure 1.3 © Acdx is licensed under a CC BY-SA (Attribution ShareAlike) license
- Figure 1.4 © David Hata is licensed under a CC BY-NC-SA (Attribution NonCommercial ShareAlike) license
- Figure 1.5 © David Hata is licensed under a CC BY-NC-SA (Attribution NonCommercial ShareAlike) license
- Figure 1.6. is licensed under a CC BY-ND (Attribution NoDerivatives) license
- Figure 1.7 © CNEU staff is licensed under a Public Domain license
- Figure 1.8 © Nancy Louwagie is licensed under a CC BY-NC-SA (Attribution NonCommercial ShareAlike) license
A body of knowledge and related skills required to undertake processes and measurements under conditions of sub-atmospheric pressure.
A “prefect vacuum” is defined as a space that is entirely devoid of any gas molecules. However, in vacuum technology, the more useful definition is a space in which the density of gas molecules is significantly reduced below that of atmospheric pressure, or where the mean-free-path is sufficient to conduct the desired vacuum process.
The sealed part(s) of pressure-controlled research or production apparatus where vacuum and/or other processes occur.
a space partially emptied of gas molecules by artificial means (vacuum pumps).
A vacuum component that moves gas molecules from a low-pressure region to a higher-pressure region. Vacuum-pump design is typically specific to its operating-pressure region, with the three main pressure regions being low vacuum (i.e., atmospheric pressure to ~1E-3 Torr), high vacuum (i.e., 1E-3 to1E-9 Torr), and ultra-high vacuum (i.e., less than 1E-9 Torr).
Decrease in density of gas.
The pressure exerted typically by the Earth’s atmosphere. Also see standard atmospheric pressure and standard temperature and pressure (STP).
Transition of a substance directly from a solid state/phase to a gas state/phase.
The transition of a liquid to a solid by the removal of heat, i.e. lowering the temperature of the liquid. An example is water, a liquid at room temperature, when it turns to ice as the temperature is lowered below its freezing point.
Delay in time.
A way of measuring how much force is acting over an area or the perpendicular force per unit area.
A pressure unit defined as Pounds per Square Inch (of Gas).
A process where surface-bound molecules are thermally desorbed from a solid or liquid surface to become part of the gas phase. Evaporation typically takes place below the boiling temperature.
The average distance which a molecule travels between two successive collisions with other molecules of the gas.
An individual particle in a vacuum that has neither a defined volume or shape. A gas molecule can be a single atom (e.g., a noble gas such as Argon, Ar) or a number of atoms bonded together to form a compound (e.g., such as water).
The number of molecules per unit volume of gas.
Conversion of a substance from the liquid state/phase to the gas (vapor) state/phase.
The term “vapor” is often used when a material may be present in several phases within a vacuum chamber at a given pressure. For example, during thermal evaporation of a metal, metal generally exists as a solid source, then as a pool of liquid metal as the temperature increases, and finally as a metal vapor evaporating from the surface of the liquid. The evaporated metal vapor will re-condense into a solid when it adsorbs onto any relatively cool surface (i.e., a substrate).
In vacuum systems, mechanical pumps are motor-driven pumps that move gas from the inlet port to outlet port using a mechanical mechanism, e.g. rotary vanes, scrolls, pistons, and diaphragms among others.
A type of dry mechanical, rough vacuum pump that utilizes a movable diaphragm element to displace and compress a volume of gas from an inlet to an outlet region.
A type of high vacuum pump that uses cold surfaces to remove gas-phase molecules by cryocondensation and/or cryosorption. Often used to refer to a vacuum pump operated with closed-cycle helium refrigeration system. Cryopump technology is based on Gifford-McMahon cryocooler which was first used to make a vacuum pump by Helix Technology Corporation in 1976.
Any one of the many parts that are required to construct a functioning vacuum system, or parts required to undertake and control a vacuum process.
Vacuum pressure regime with pressures between 760 Torr and 1E-3 Torr.
The amount of gas that must be removed from the chamber in a vacuum system by the vacuum pump(s). It is typically measured in torr-liters per second, cubic feet per minute, or cubic meters per hour.
One of several types of electrical or mechanical devices used to measure pressure and/or gas density at various locations of a vacuum system.
The pressure exerted by a particular species of gas molecules. According to Dalton’s law, the sum of the partial pressures of all the component species in a mixture is equal to the total pressure.